Abrasive Blasting
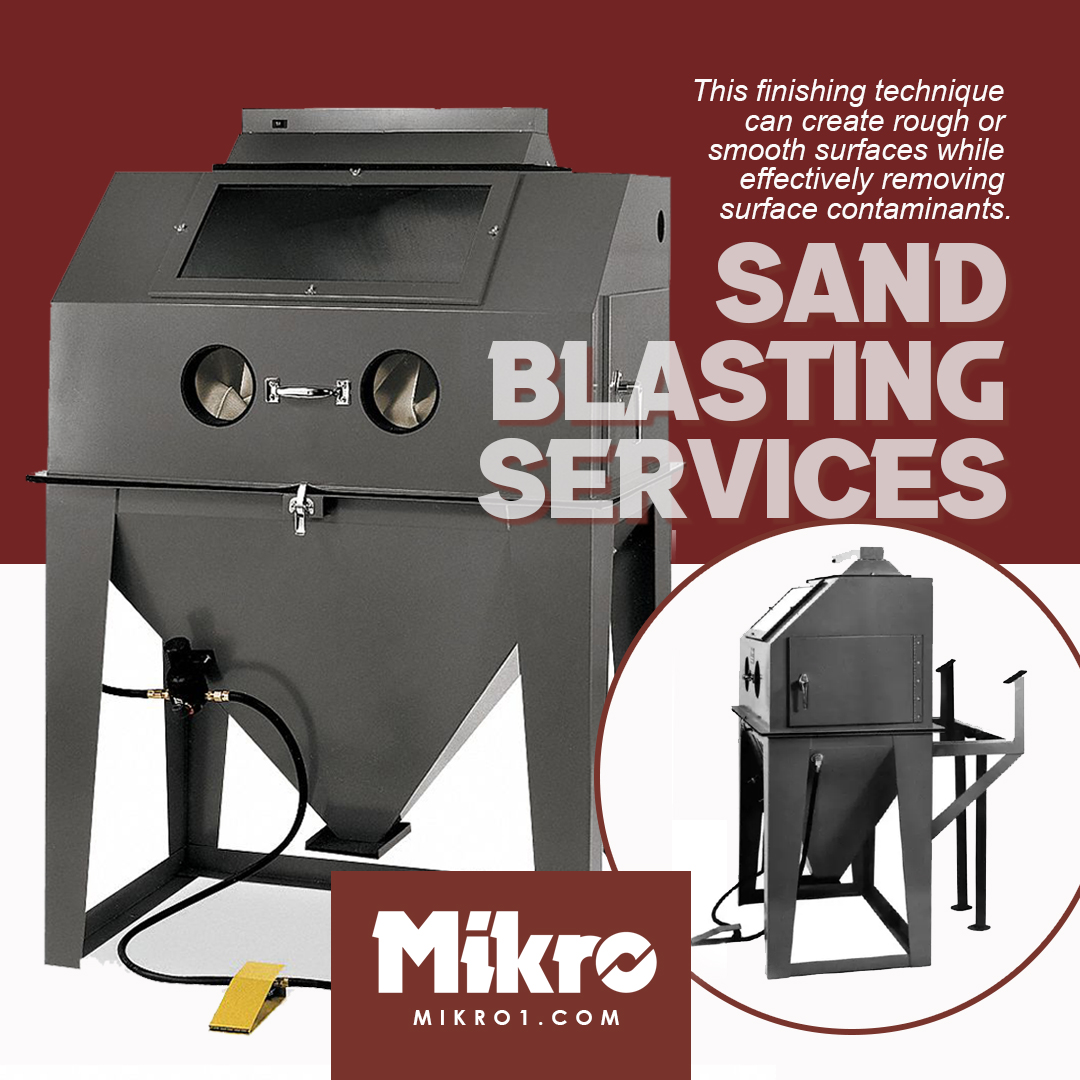
Abrasive blasting, or sandblasting, is a common and cost-effective method to prep surfaces for finishing. Using pressurized air, the sanding medium is blasted over the surface of a workpiece to remove contaminants and either toughen or smooth a surface. Sandblasting is common for metal and glass workpieces but can be used for other materials. Because of the danger of inhaling the media at close range, sandblasting equipment must be carefully controlled. Strict quality assurance programs are conducted for abrasive blasting media to ensure it is safe to use for the workpiece and for the equipment operators.
Abrasive blasting media can be used for wet or dry blasting. While sand is the most common media for abrasive blasting. Other gritty materials such as steel grit, copper, walnut, and synthetic abrasive blasting media are also common. The process is primarily used to prep surfaces for further painting or finishing, as it is not as effective for deburring workpieces with holes or crevices as vibratory finishing.
Sandblasting is commonly used for:
- Burr removal
- Oxide removal
- Surface preparation
- Cutting
- Etching
- Abrading
- Surface cleaning
Many of our clients prefer sandblasting to other finishing methods because of its low cost and effectiveness in both cleaning and deburring. At Mirko, we carry a quality line of abrasive blasting equipment and media for all of your facility needs. All of the manufacturers we carry must meet stringent quality standards, as we believe in providing the very best for our clients.
If you are not ready to invest in abrasive blasting equipment for your job site, talk to us about the Mikro Job Shop. Our Job Shop offers fast, reliable sandblasting services onsite as a convenience for you. We also offer vibratory finishing, degreasing, and other cleaning services to complete the process. Shipment-ready workpieces are guaranteed when you work with our top engineers and industry leaders at the Job Shop. We also promise a quick turnaround time and access to the best equipment available.
Mikro works with the following manufacturers for their quality abrasive blasting media and equipment:
Pressure Blast
Wet and dry blast cabinets, automated systems
Blast-It-All
Cabinets, rooms, automatics, pressure systems
Econoline
Cabinets, rooms, automatics, pressure systems
Abrasive Blasting
Abrasive blasting also known as sandblasting is a common and cost-effective method to prep surfaces for finishing. Using pressurized air, the sanding medium is blasted over the surface of a workpiece to remove or clean contaminants and either toughen or smooth a surface. One major advantage of this process is that it keeps the surface intact while removing everything else.
Abrasive blasting media can be used for wet or dry blasting. While aluminum oxide is the most common media for abrasive blasting. Other gritty materials such as steel grit, glass, walnut, and synthetic abrasive blasting media are also common. The process is primarily used to prep surfaces for further painting or finishing, as it is not as effective for deburring workpieces with holes or crevices as vibratory finishing.
There are two main types of abrasive blasting; wet and dry blasting.
Sandblasting is commonly used for:
- Burr removal
- Oxide removal
- SurPreparationation
- Cutting
- Etching
- Abrading
- Surface cleaning
- Remove rust and corrosion
- Smoothen rough casting and edges
There are two processes of abrasive blasting:
- Air-Driven: It is best suited for metal surfaces to prevent moisture build-up and avoid water intrusion.
- Water-Driven: It reduces surface deterioration and is best suited for precision applications
A benefit of abrasive blasting is that it does not chemically react with the material being cleaned. Also, it is eco-friendly, efficient, quick, cost-effective, and prepares metal surfaces for coating application which is why many of our clients prefer this method to other finishing methods.
Due to the danger of inhaling the dust at close range or eye irritation from the fine particles of sand, sandblasting equipment must be carefully controlled and proper safety gear must be worn during the sandblasting process. The manufacturers we work with conduct strict quality assurance programs for abrasive blasting media to ensure it is safe to use for the workpiece and the equipment operators.
We carry a quality line of abrasive blasting equipment and media for all of your facility’s needs. All of the manufacturers we carry must meet stringent quality standards, as we believe in providing the very best for our clients.
If you are not ready to invest in abrasive blasting equipment for your job site, talk to us about the Mikro Job Shop. Our Job Shop offers fast, reliable sandblasting services onsite as a convenience for you. We also offer vibratory finishing, degreasing, and other cleaning services to complete the process. Shipment-ready workpieces are guaranteed when you work with our top engineers and industry leaders at the Job Shop. We also promise a quick turnaround time and access to the best equipment available.